大塚化学は、チタン酸カリウム繊維「ティスモ(TISMO)」の優れた特性と各種熱可塑性樹脂の特性を巧みに組み合わせた独自の高機能複合材料「ポチコン(Potassium Titanate Compound)」の特長を生かしたままで、ポチコンペレットを熱溶解積層法(FFF)用にフィラメント化している。
2022年からは大塚化学のTISMO配合3Dプリンター用樹脂複合材料「ポチコンフィラメント」と、業界トップレベルの高速・高精度造形を実現するグーテンベルクのFFF式3Dプリンター「G-ZERO」を用いた試作造形と、造形品の物性評価を開始。
さらに2023年両社は資本業務提携を行い、各種製造業が抱える社会的課題を解決するため、国内の樹脂3Dプリンティング分野で初となる材料と機械の共創によって、G-ZEROによってポチコンフィラメントの性能を引き出した高速・高強度・高精度造形を実現しつつ、ロボット部品や自動車部品など各種産業分野での適用展開を進めている。
ここでは、本年7月から発売を開始した高速・高強度・高精度を実現する大型産業用3Dプリンター「G-ZERO L1」と、材料×機械の共創による樹脂3Dプリンティングの産業展開について、大塚化学 化学品事業本部 ダイレクターでグーテンベルク 社外取締役の稲田幸輔氏と、グーテンベルク 開発部 統括部長 兼 製造・生産技術部門 プロダクトマネージャーの梶 貴裕 氏に話を聞いた。
高機能樹脂複合材料フィラメント
大塚化学のTISMOは繊維長10~20μm、繊維径0.3~0.5μmと極めて微細・高アスペクト比で、高強度・高剛性、優れた摩擦摩耗特性、断熱性、耐熱性、耐薬品性などの特徴を有する(図1)。同社が1980年ごろに開発したポチコンは、TISMOの各種特性と、各種熱可塑性プラスチックスの特性を巧みに組み合わせた機能性樹脂複合材料で、大別して以下のような特長を持つ。
①樹脂中の繊維の分散状態がミクロ単位で均一なため、従来は極めて困難とされていた極小・超薄肉製品の超精密成形が可能(ミクロ補強性)
②アルミや快削鋼を削らず(相手材への攻撃性が低く)、無潤滑摺動が可能なため、摺動部品に最適
③TISMOが極めて微細な繊維であることから射出成形品細部にまで分散し、優れた寸法精度と寸法安定性を発揮
④TISMOを配合して作られるポチコン成形品は金型転写性が高く、鏡面状態の平滑面が得られる
⑤TISMOの剛性、強度、サイズなどに由来する、優れたリサイクル性を有する
大塚化学では2016年頃から、上述の利点を有するポチコン材料について、3D造形用としての展開を開始した。TISMOを配合し、均一な径のフィラメント作製を実現。市場で主流のFFF方式によって、TISMO入りのポチコンフィラメントは、①造形品のミクロ補強性、②プリンターノズルの摩耗低減、③造形品の優れた寸法精度と寸法安定性、④造形品の優れた表面平滑性、といったメリットを提供している。
以降、他の材料では得られない機能性や、造形条件の最適化、樹脂パラメータの最適化を検討しながら、ポチコンフィラメントという材料と、3Dプリンターやノズルといったハード、さらにはスライサーなどのソフトウェアという三位一体による開発を重ねている。
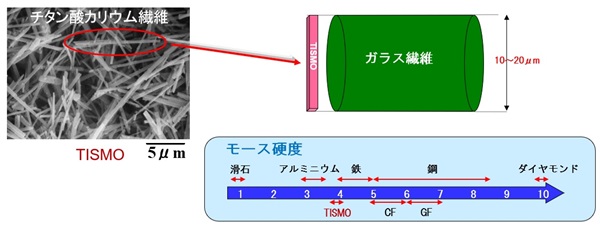
高速・高精度3Dプリンター
グーテンベルクが2022年に開発・販売開始したFFF方式採用の高速・高精度3Dプリンター「G-ZERO」(図2)は、造形の速さを左右する要素の一つであるツールヘッドのノズル最大移動速度が500mm/s、プリントヘッド最大加速度20000mm/s2と、同価格帯の市場にある3Dプリンターに比べて10倍の速度と20倍程度の加速度を実現している。
G-ZEROの高速性と精度を実現する技術としては、ベースプレートの1枚板化といった筐体の高剛性/高精度化のほか、X軸、Y軸の駆動に採用した、ツールヘッドを載せる直動案内(リニアガイド)が1本あるだけで可動部を大幅に軽量化できるMIT考案の「Core-XY」方式や、軽量性と精度を両立したツールヘッドなどによる、駆動部品の軽量化が挙げられる。
さらには、加速の際の過剰な吐出を抑制する「押出圧力予測制御」や、加速の際の振動による品質低下を防ぐための「共振を抑制する入力成形制御」も高速造形での高精度化の肝となっている。
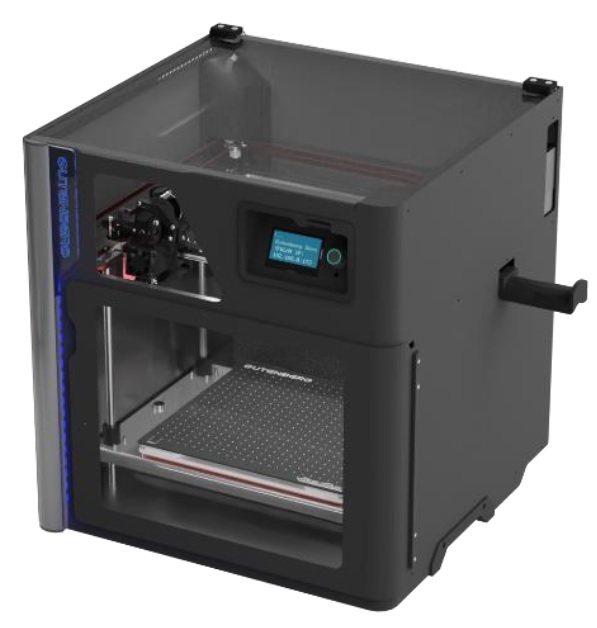
材料×機械の共創による樹脂3Dプリンティング技術の向上
大型産業用3Dプリンター「G-ZERO L1」の開発
資本業務提携を機に両社は、ユーザーにとってより多くのメリットを提供できる装置開発を推進、G-ZEROの業界トップレベルの速度と精度を継承・発展(最高速度700mm/s、最高加速度30000mm/s2、積層ピッチ50~200μm)させつつ、造形エリアを約2倍の360mm×250mm×235mmまで拡大した大型産業用3Dプリンター「G-ZERO L1」(図3)を開発、本年7月から発売を開始した。ポチコンフィラメントとの組み合わせにより、これまで分割せざるを得なかった大型の部品も高強度に、高精度・高速で造形でき、ユーザーの作業効率を向上できる。
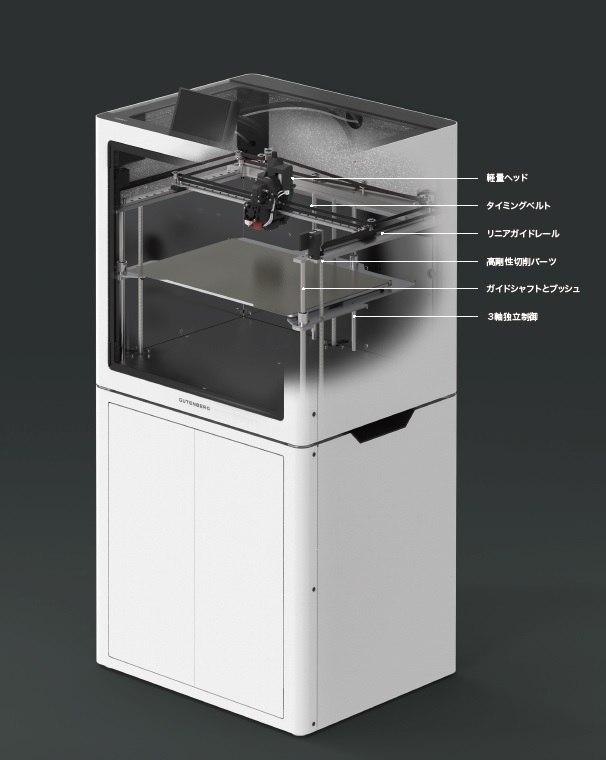
材料劣化を防ぐ除湿ユニット
G-ZERO L1では装置の下部構造として特殊機構のドライボックス(除湿ユニット)を搭載した(図4)。大塚化学の知見をもとに1年間を費やして開発したもので、品質劣化の原因となる湿気からフィラメントを保護するため、ドライボックス内にセットされたフィラメントが外気に触れることなく印刷ヘッドに自動で送られる。
稲田氏は「フィラメントの保管の仕方は造形性や造形精度、造形強度を左右する最も大きな要因。この除湿ユニットの搭載によって、産業向けで不可欠な「造形の繰り返し品質」を担保できている」と語る。
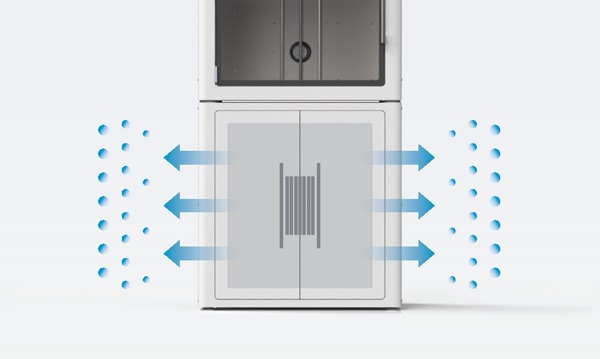
高速・高精度造形を保持する高耐久設計
高速移動によるレールへの負荷を下げる軽量ヘッドでは今回、少し重量がかさんだとしても精度を優先させ高剛性化による繰返し精度の安定性を向上できる設計としている。そうした点からは樹脂パーツには今後、高剛性で高精度なポチコンフィラメントによる造形品も採用していく。梶氏は、「ホットエンドのところで溶融した樹脂の吐出安定性が得られるように、ヘッドの材料が通過する穴も工夫している」と述べる。
G-ZEROと同様に、ツールヘッドをのせた直動案内(リニアガイド)と上下動のガイドシャフト/ブッシュはいずれもTHK製を、X軸、Y軸の駆動に使うタイミングベルトはゲイツ・ユニッタ・アジア製を採用している(図5)。高速造形において常に負荷のかかる可動部には信頼性の高いメーカーによる高品質な部品を採用し長期にわたり高い耐久性と精度を担保している。「つまり、これで造形精度が出ない場合には装置全体を組み上げているグーテンベルクのせいということになる。高品質部品を採用することで責任の所在を明確にして、各パーツを微調整しつつ組み上げる社内の技術の底上げを図っている。結果、稼働時の装置本体の共振なども少なく、非常に静かな造形を実現している」と語る。
高速・高精度造形を支える装置骨格のフレームには現在、外注した高剛性切削パーツを使っているが、現在羽田に新工場の設立を進めており、マシニングセンターや三次元測定機を導入して、年内にも削り出しの高剛性フレームの内製に切り替える予定だ。フレームに限らず要素部品の内製化を進め、品質を担保するとともに図面の流出を防ぐ考えだ。
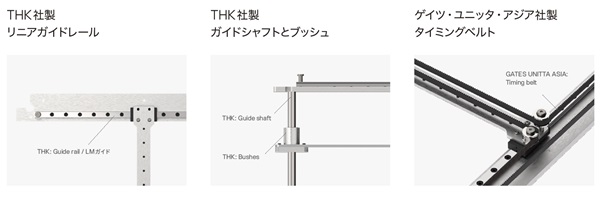
材料×機械の共創による造形強度・精度の向上
射出成形に迫る造形強度
G-ZEROとポリフェニレンスルフィド(PPS)にティスモを20%コンパウンドしたポチコンフィラメントによる高い層間強度に加え、XY方向においては引張強度110MPa、曲げ強度210MPaと同素材の射出成形品を上回る造形強度を実現しており、他社製品の組み合わせと比較すると実に2倍以上の強度が得られている(図6)。これはダイナミックな機構部品にも十分使用できる数値で、ロボットの部品としても使われるベアリングのリテーナー(保持器)なども適用が可能と見られる。

平均誤差率0.18%の高い造形精度
造形品の精度比較の結果、G-ZEROとポチコンフィラメント(HARD PPS)を組み合わせた造形品の平均誤差率は0.18%と、他社製のプリンターと材料による造形品に比べ圧倒的に高い寸法精度を実現している(図7)。
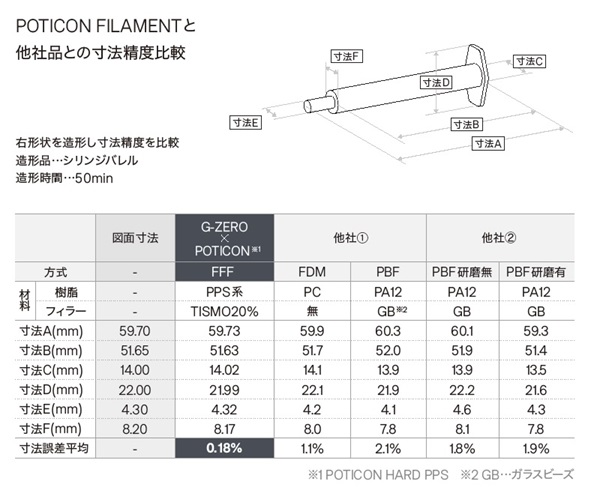
材料×機械の共創による今後の展開
両社ではすでに、ポチコンフィラメントとG-ZERO L1との組み合わせでさまざまな造形品を作り、物性評価を進めている。
たとえばPAベースのポチコンフィラメント(白色および黒色)で造形したダンベル(図8)は真っすぐに立てることが可能で、6月19日~21日に東京・有明の東京ビッグサイトで開催された「ものづくりワールド [東京] 2024:次世代3Dプリンタ展」のグーテンベルクブースで展示した際、多くの来場者の関心を集めた。この造形にはポチコンフィラメントとG-ZERO L1との組み合わせによって、0.1mm厚のA4サイズの均一なシートを高い繰返し精度で造形できる技術がベースにある。ポチコンフィラメントはフィラーが均一に入っていて造形品が反りにくく、G-ZERO L1との組み合わせで、強度低下につながるサポート材を使わずに高精度・高強度造形を可能にしている。
稲田氏は、「このところ3Dプリンティングの材料と装置に対してリテラシーの高い設計者が増えてきているが、そうした設計者に対してブースで、射出成形品に比べZ-X方向の曲げ強度こそ8割程度となるもののX-Y方向の曲げ強度は3割高いというポチコンフィラメントの物性値を開示したところ、さらに驚かれる結果となった」と言う。
PPSベースのポチコンフィラメントとG-ZERO L1との組み合わせではまた、ポチコンHARD PPSの耐熱性と強度を生かして、250mm×230mm×120mmと大きなサイズの入れ子構造の真空成形の型(図9)を24時間程度で試作している。「他社の材料と装置でこの造形を行ったとしたら200Vの電源で3日間程度を要するが、G-ZERO L1とポチコンフィラメントの組み合わせでは100V電源、1日で造形できる。作業時間を短縮できる上、電力使用の低減、電気代の節約につながり、環境負荷低減、サステナビリティに貢献できると言える」と稲田氏。
今回A4判サイズの造形が可能なG-ZERO L1を販売開始したが、自動車部品やロボット部品などのさらに大型の部品を分割せずに造形したいとのニーズも両社に寄せられており、より大型の産業用プリンター「G-ZERO X1(仮称)」の開発もすでに進めている。梶氏は「大塚化学はポチコンフィラメントに関し常に分析・品質管理を徹底し高精度・高品質を追求している。グーテンベルクもまた、材料に対応した繰返し精度の高い造形を実現できる装置の組み上げ技術の底上げを図っており、ハード×ソフト×マテリアル×人材が一体となった開発体制となってきている。両社の国内設計・国内生産だから可能なユーザーのトータルサポートを行いつつ、ユーザーの声を聞きながら、ユーザーが要求する機能に最適な材料と造形方法を突き詰めていくことで、ロボットをはじめ各種産業分野での3Dプリンティングの適用を広げていきたい」と述べている。